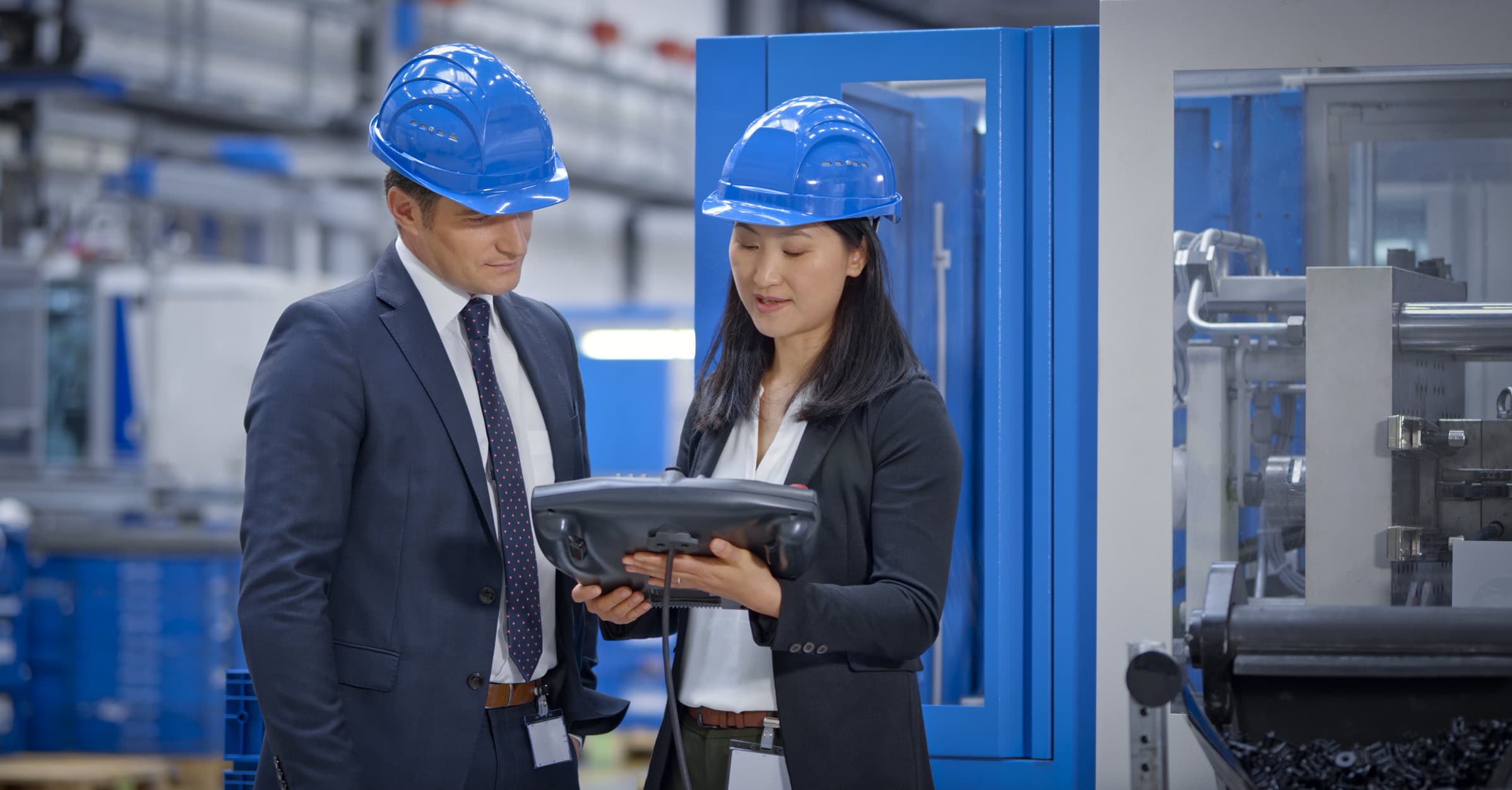
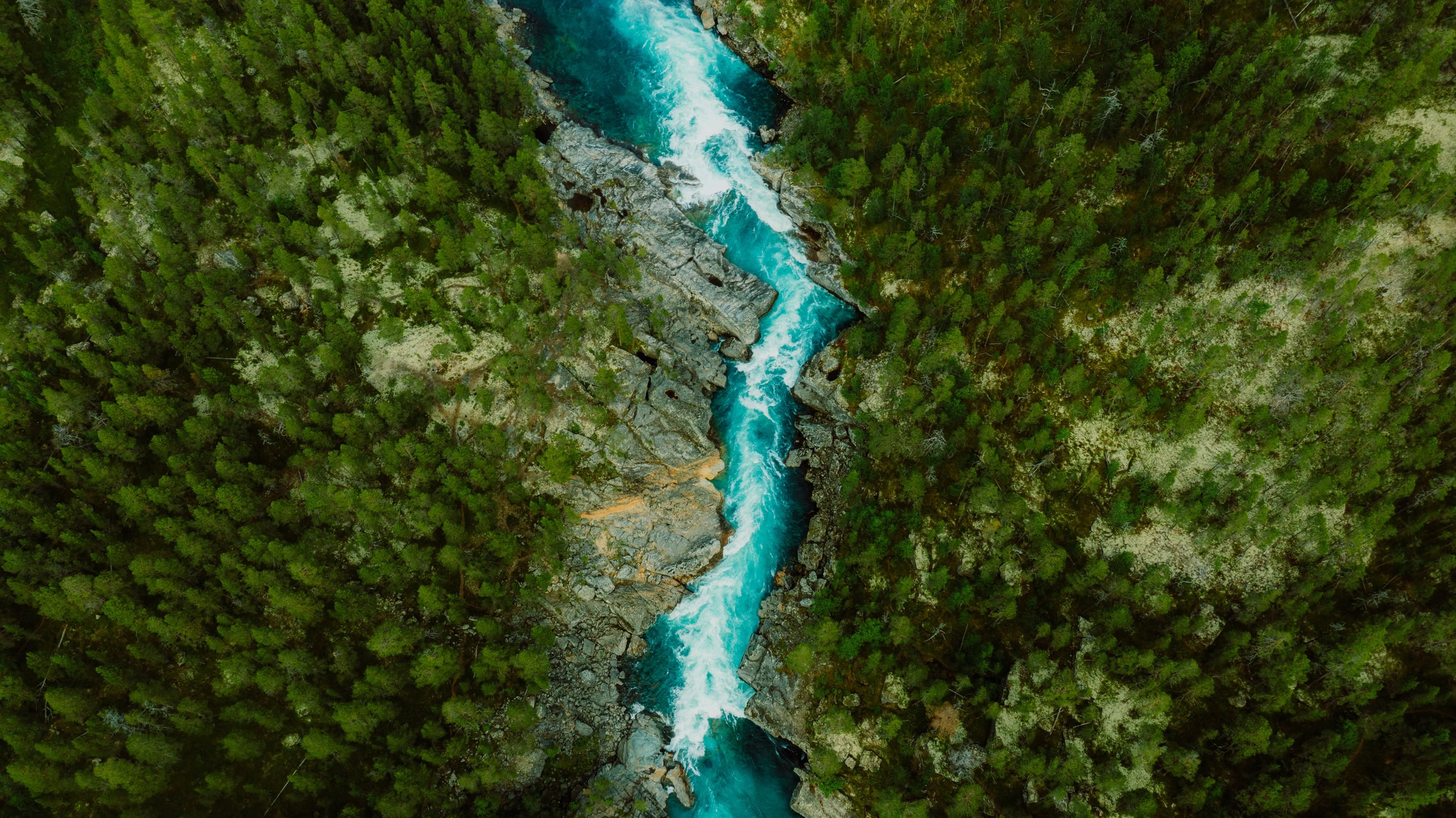
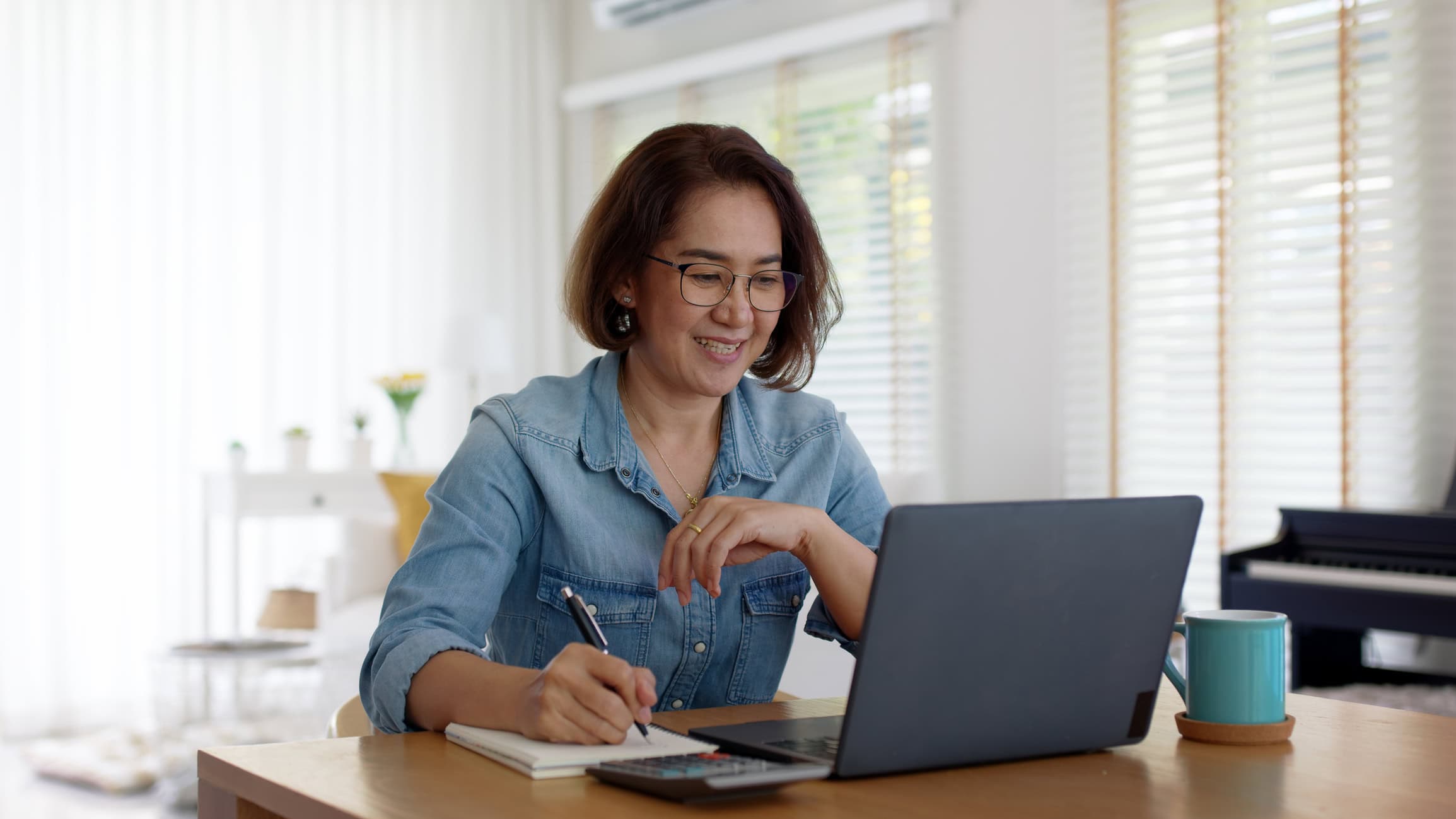
ASSESSMENT
Kick-start your transformation journey
Set the stage for your organisation's transformation journey by first assessing the state of your current capabilities
Learn howSUSTAINABILITY
Identifying sustainable solutions
We help manufacturers assess their sustainability state-of-readiness
Learn howTRAINING AND CERTIFICATION
Lead the change
Be a leading-edge consultant driving industrial transformation globally
Learn howglobally
In focus
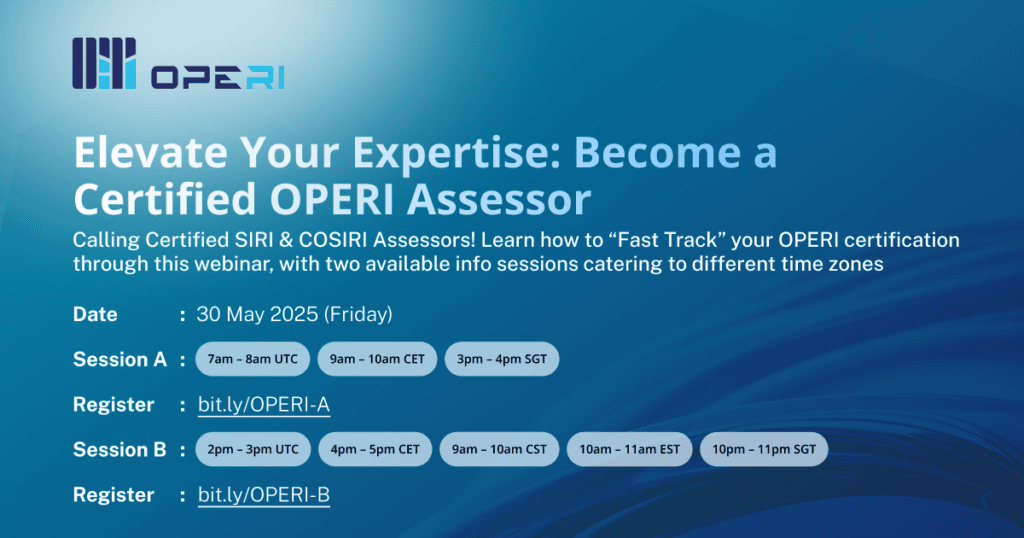
The Next Step in Your INCIT Journey: Discover the Fast Track to OPERI Certification
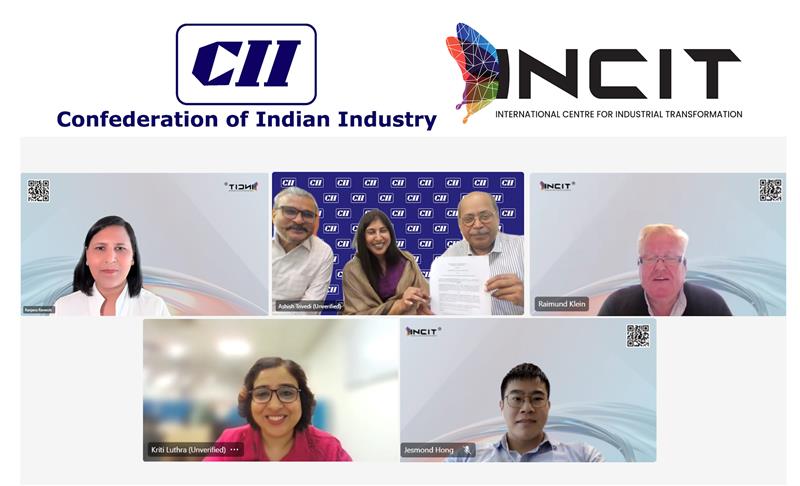
Confederation of Indian Industry (CII) and INCIT Signed Strategic Cooperation Agreement to Accelerate Industrial Transformation in India
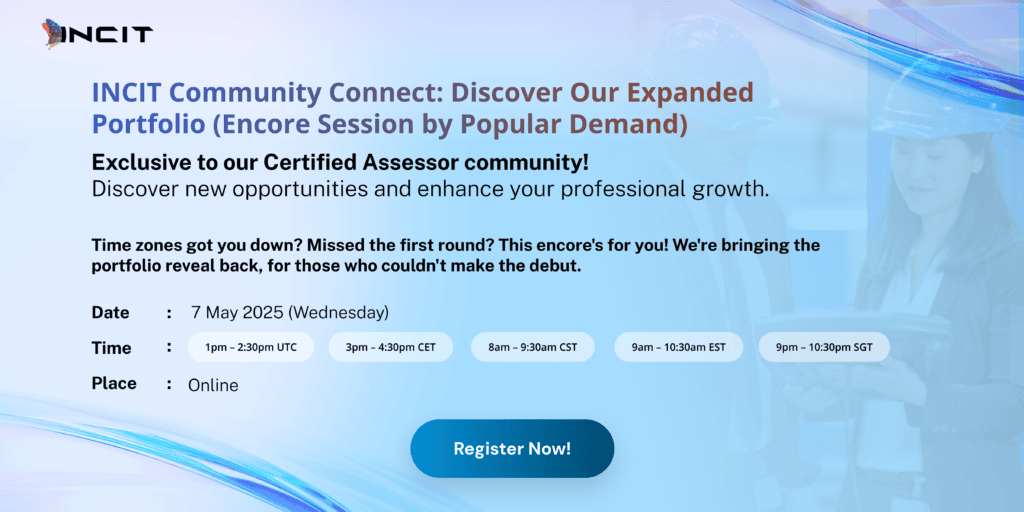
Back by Request, Second Chance to Connect: INCIT Returns with Encore Webinar on Portfolio Expansion
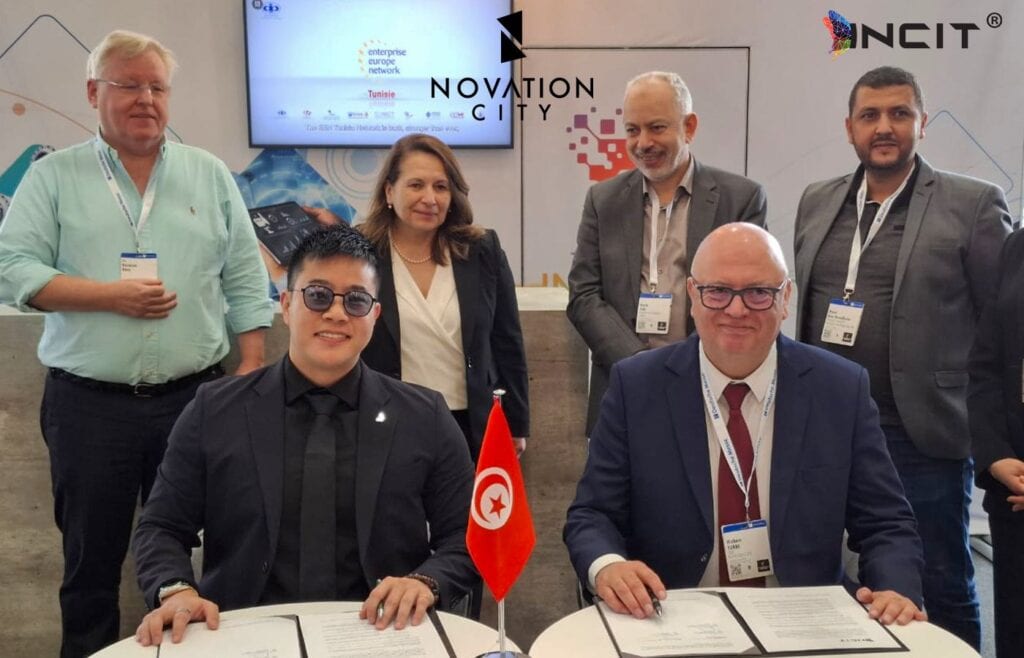
A Strategic Milestone for the African Industry: INCIT and Novation City Partner at Hannover Messe 2025
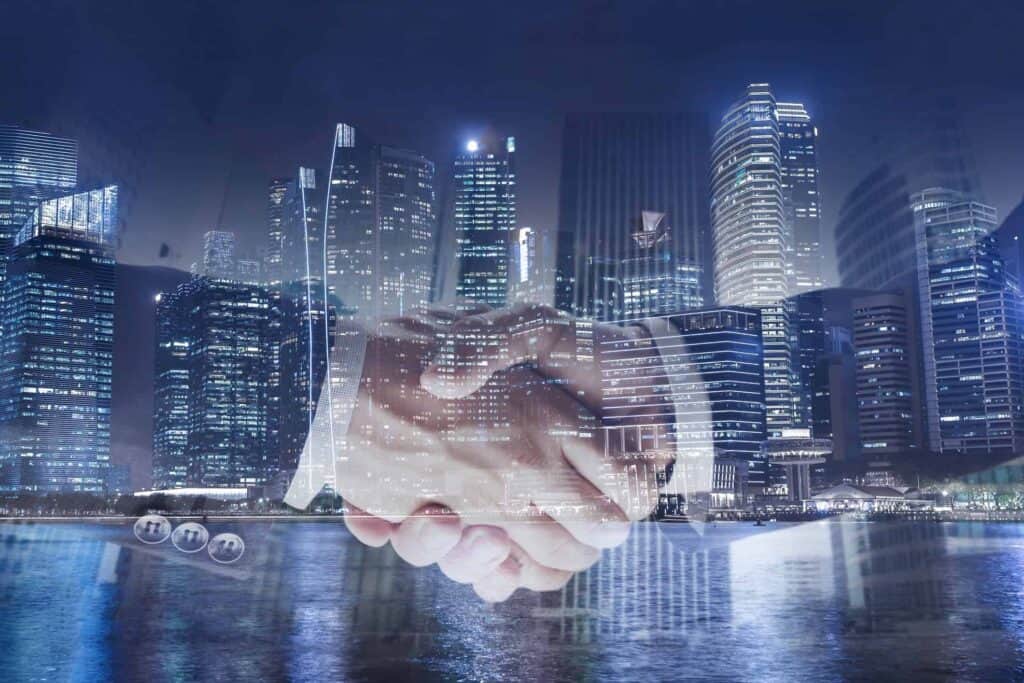
INCIT and Eficens Systems Announce Strategic Partnership to Accelerate Global Industrial Transformation
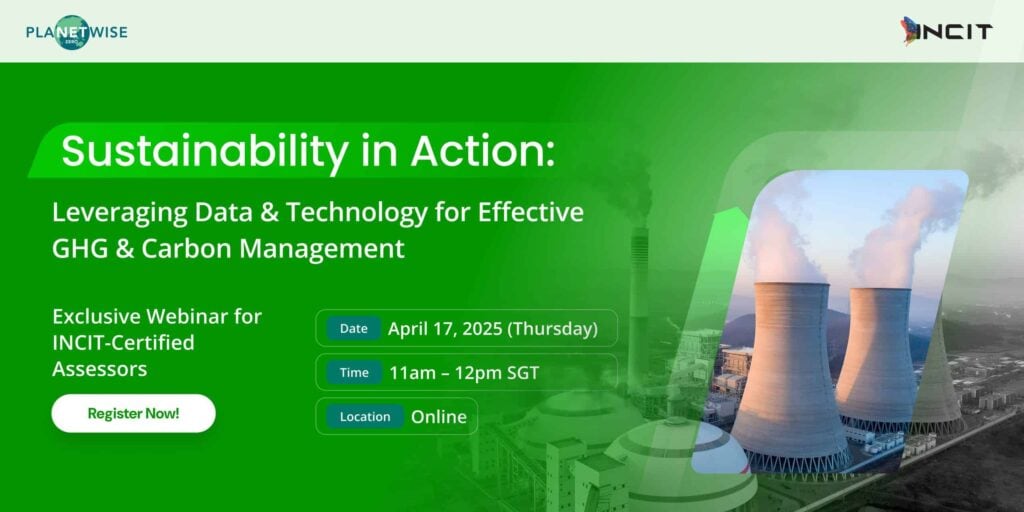
Sustainability in Action: Leveraging Data & Technology for Effective GHG & Carbon Management
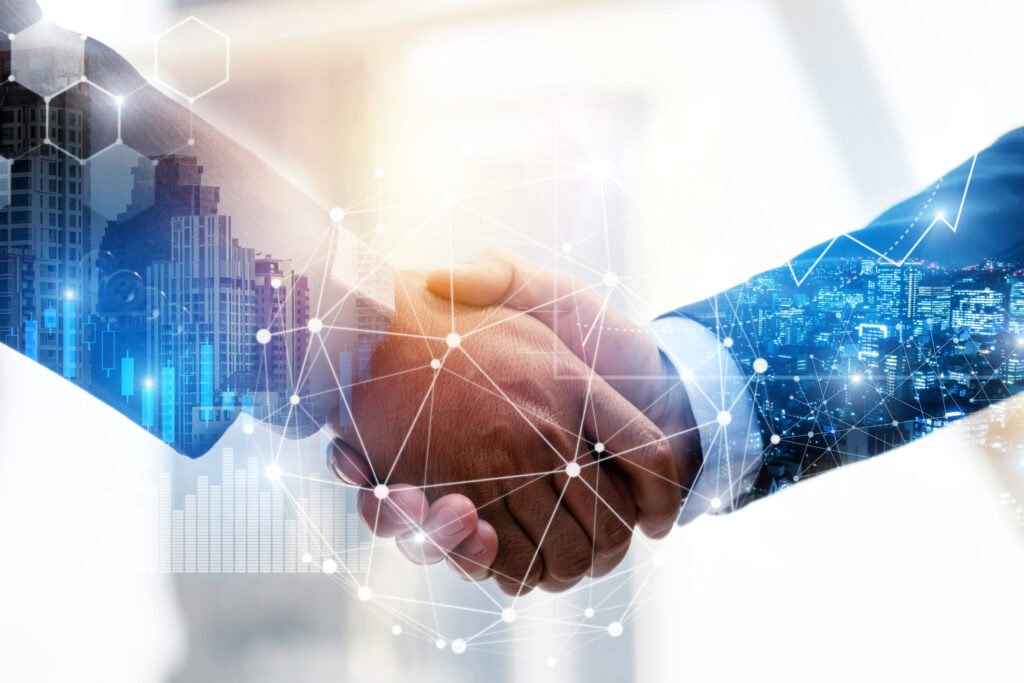
Hitachi and INCIT Partner to Advance Digital Transformation with Smart Industry Readiness Index (SIRI) and XIRI-Analytics
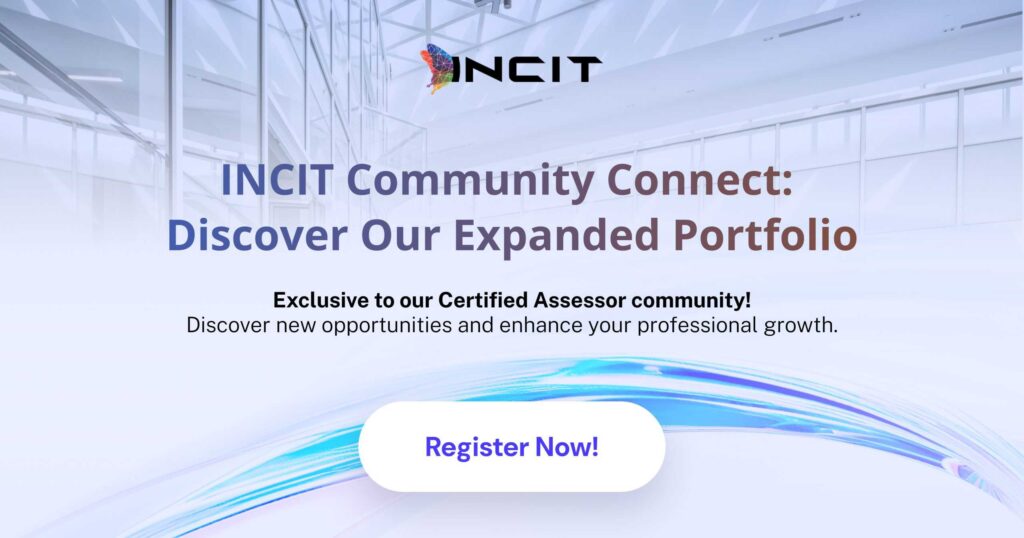
Strengthening Partnerships: INCIT Announces Exclusive Webinar for Assessor Community on Portfolio Expansion
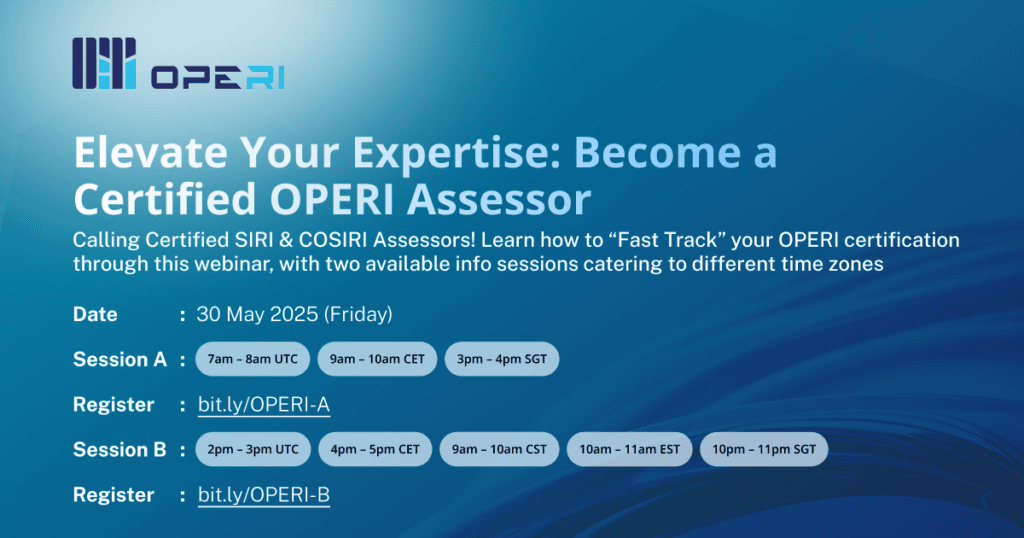
The Next Step in Your INCIT Journey: Discover the Fast Track to OPERI Certification
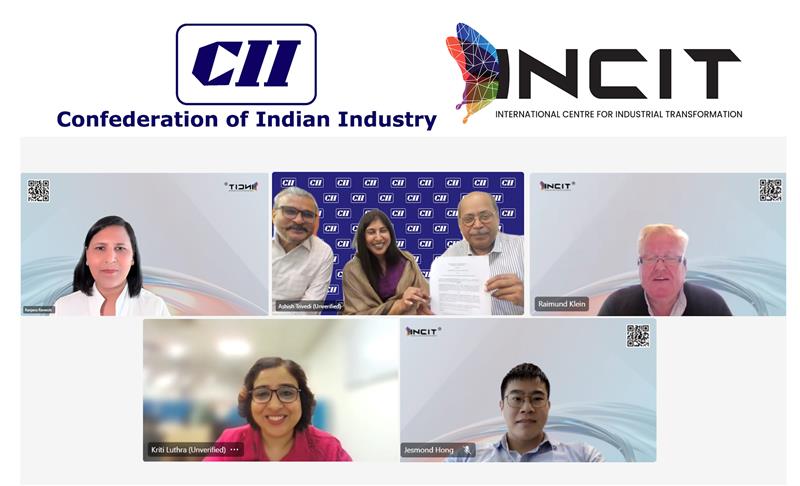
Confederation of Indian Industry (CII) and INCIT Signed Strategic Cooperation Agreement to Accelerate Industrial Transformation in India
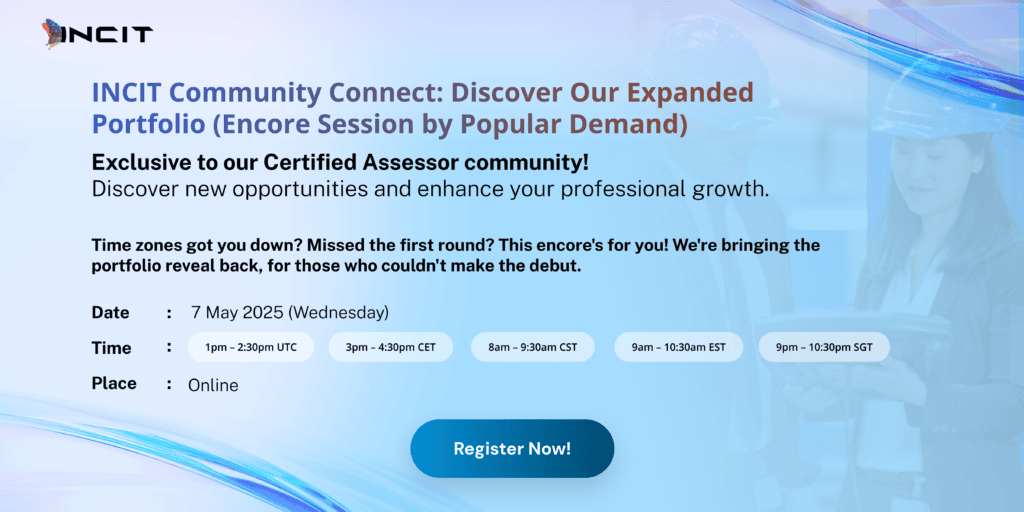
Back by Request, Second Chance to Connect: INCIT Returns with Encore Webinar on Portfolio Expansion
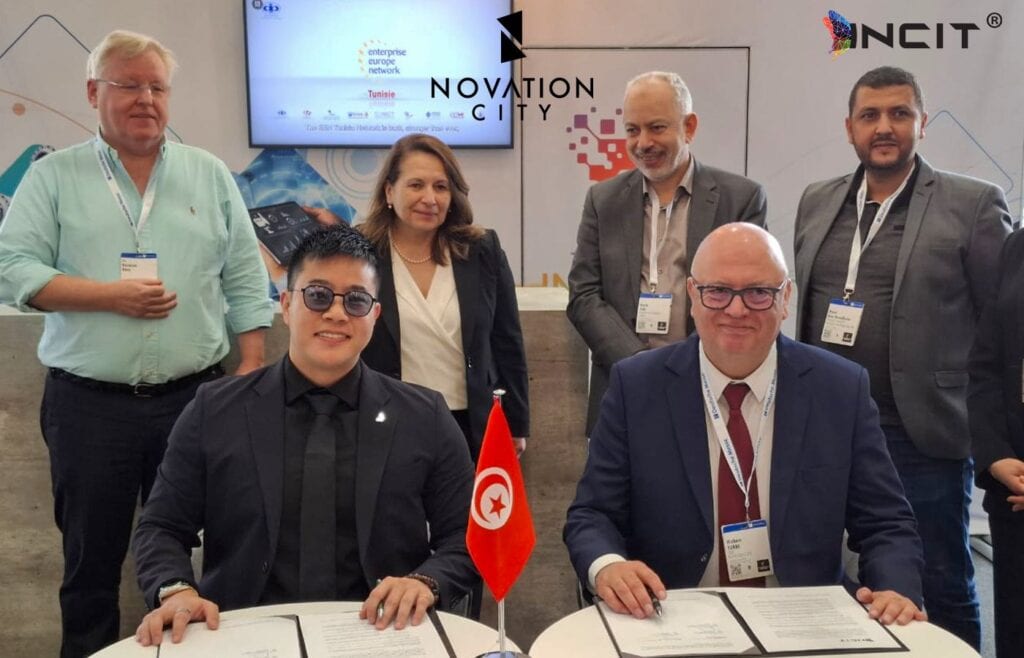
A Strategic Milestone for the African Industry: INCIT and Novation City Partner at Hannover Messe 2025
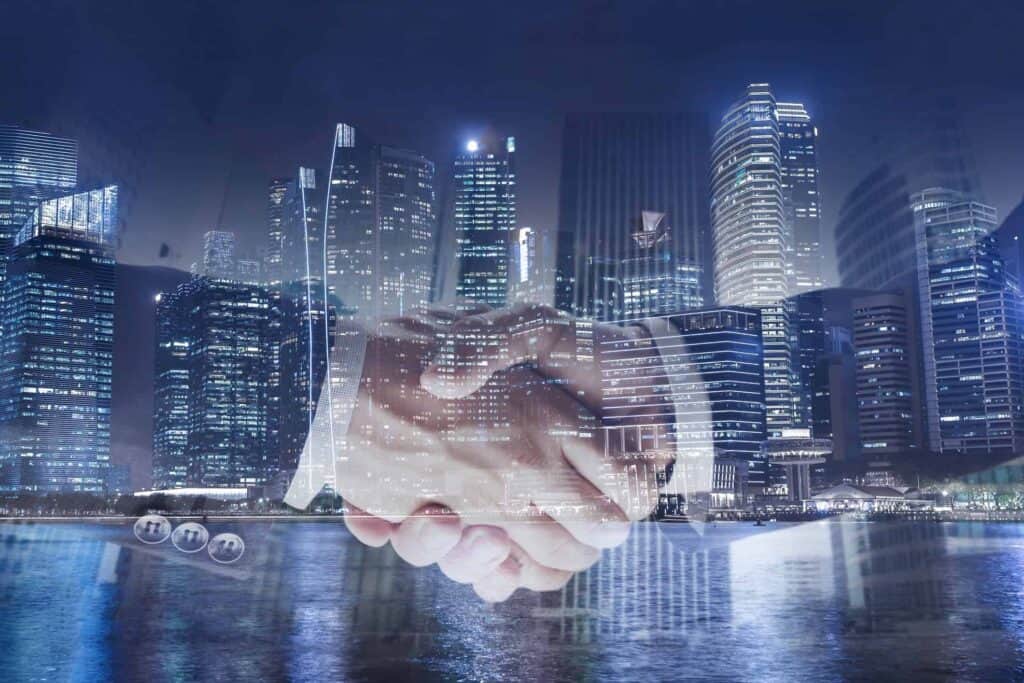
INCIT and Eficens Systems Announce Strategic Partnership to Accelerate Global Industrial Transformation
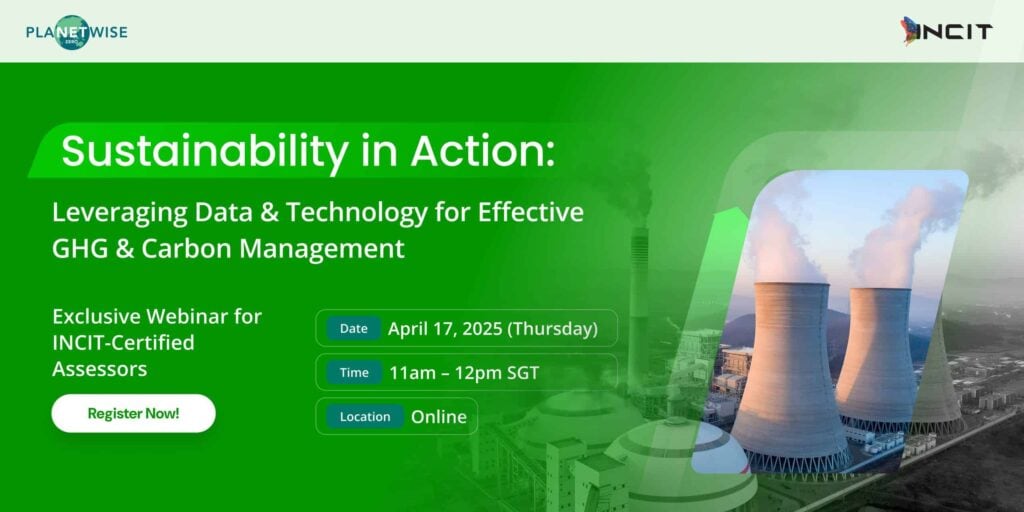
Sustainability in Action: Leveraging Data & Technology for Effective GHG & Carbon Management
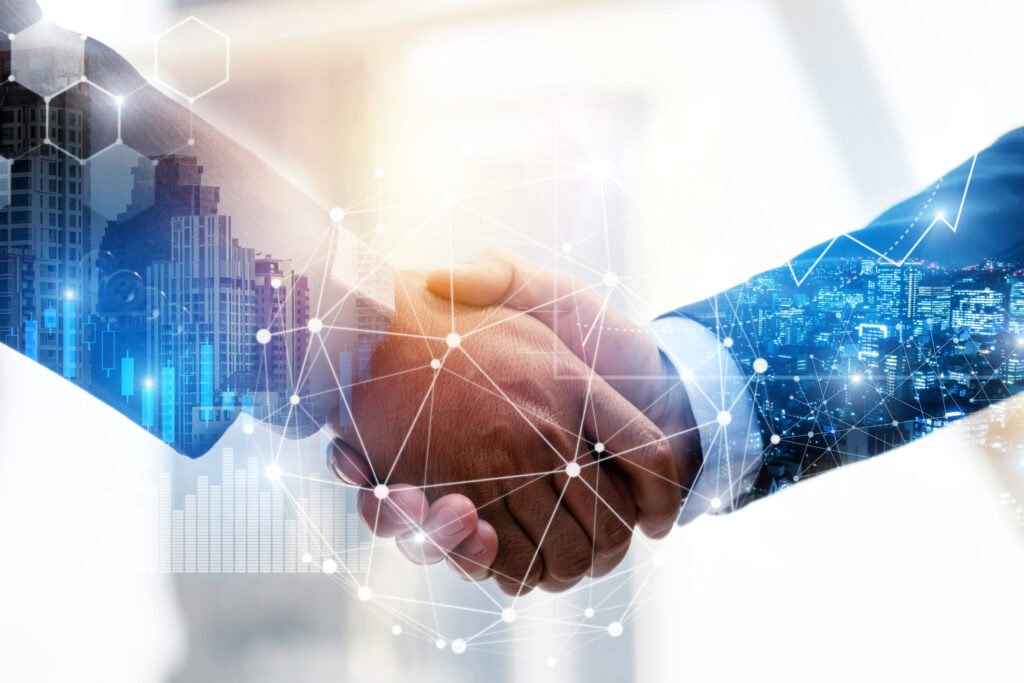
Hitachi and INCIT Partner to Advance Digital Transformation with Smart Industry Readiness Index (SIRI) and XIRI-Analytics
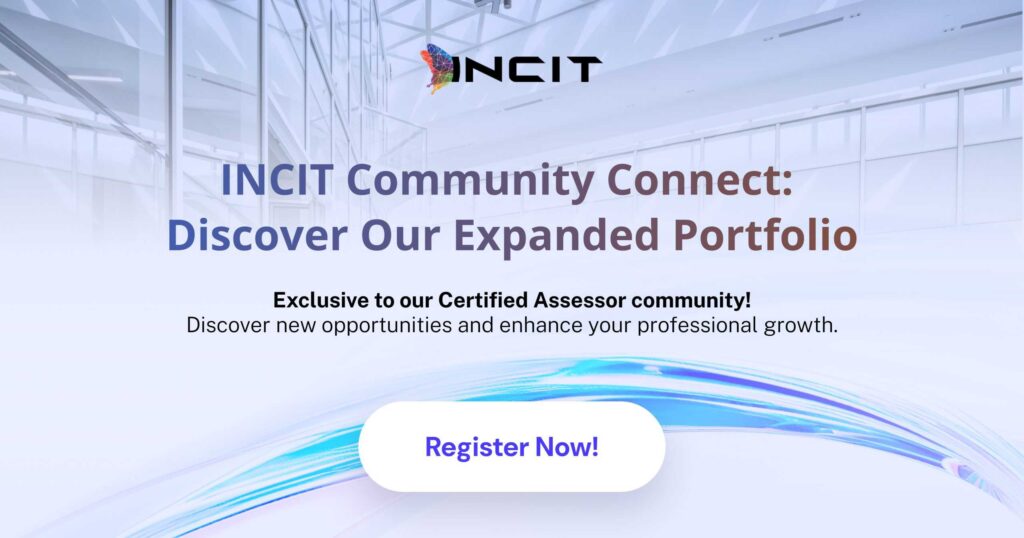
Strengthening Partnerships: INCIT Announces Exclusive Webinar for Assessor Community on Portfolio Expansion
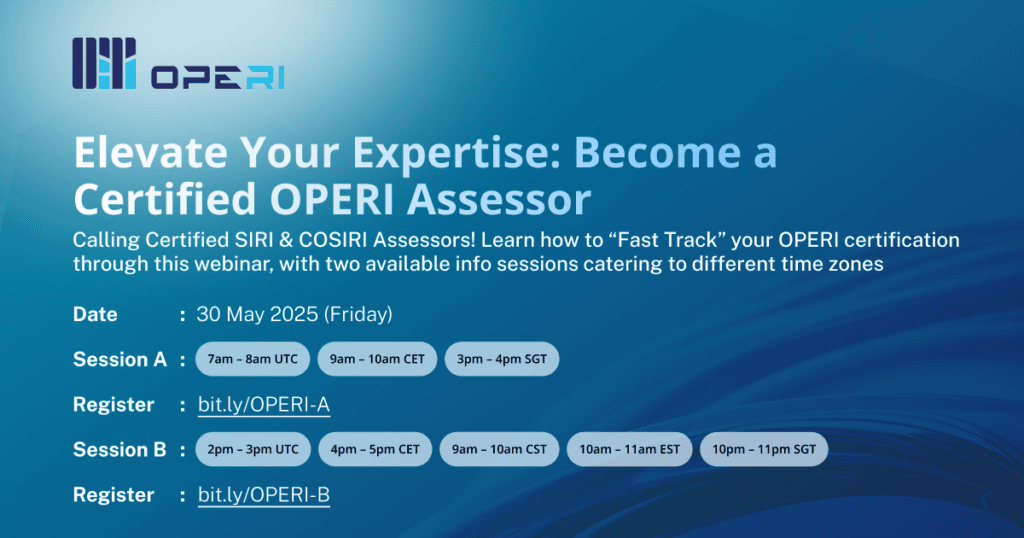
The Next Step in Your INCIT Journey: Discover the Fast Track to OPERI Certification
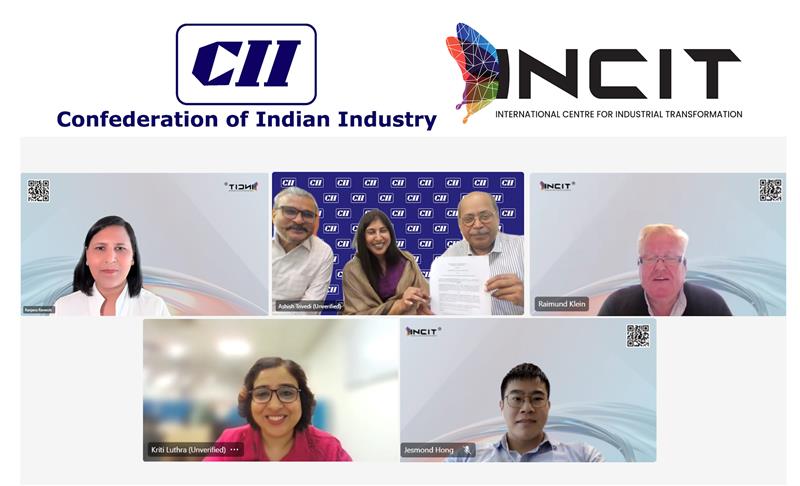
Confederation of Indian Industry (CII) and INCIT Signed Strategic Cooperation Agreement to Accelerate Industrial Transformation in India
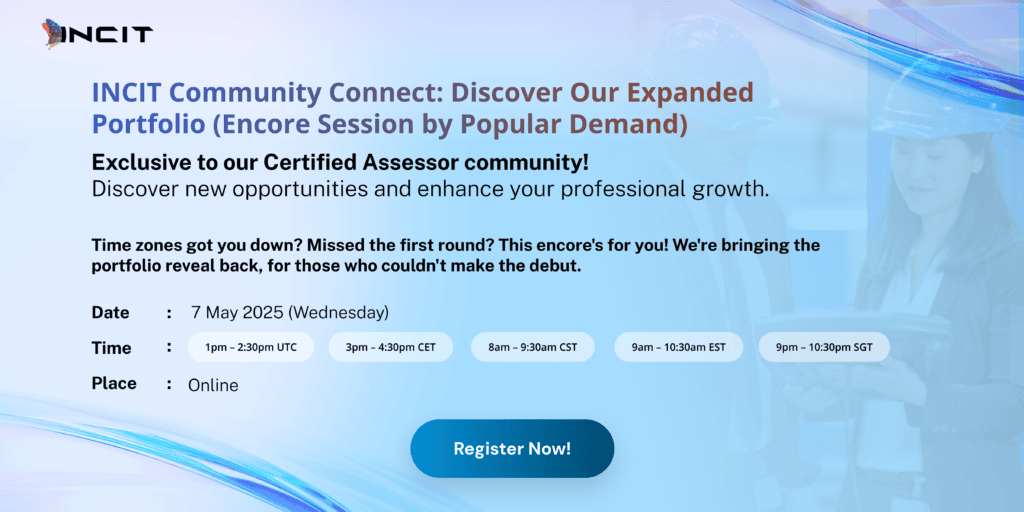
Back by Request, Second Chance to Connect: INCIT Returns with Encore Webinar on Portfolio Expansion
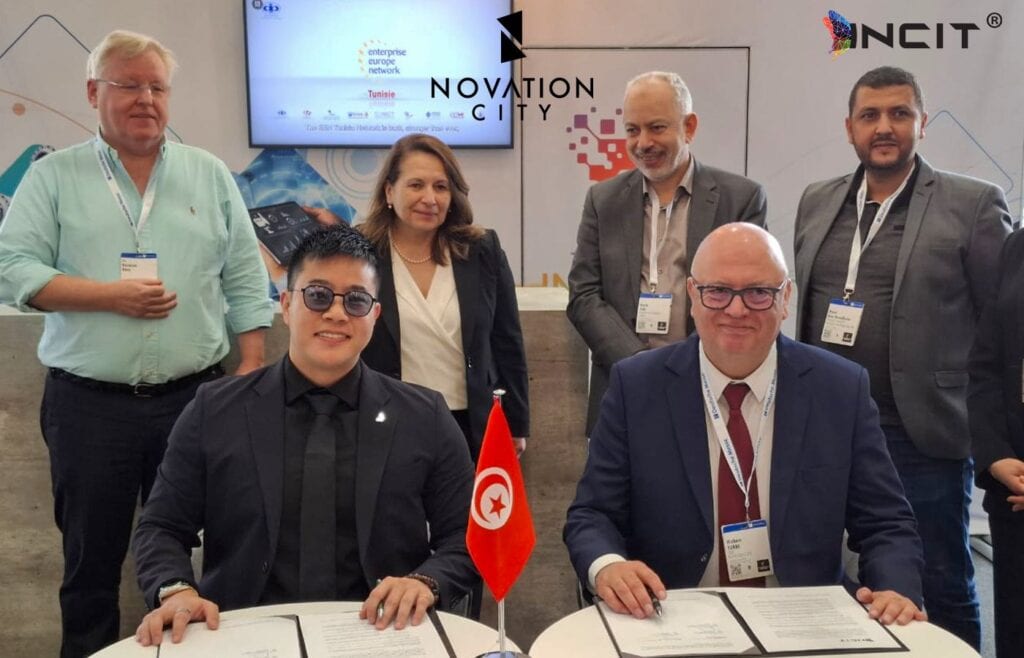
A Strategic Milestone for the African Industry: INCIT and Novation City Partner at Hannover Messe 2025
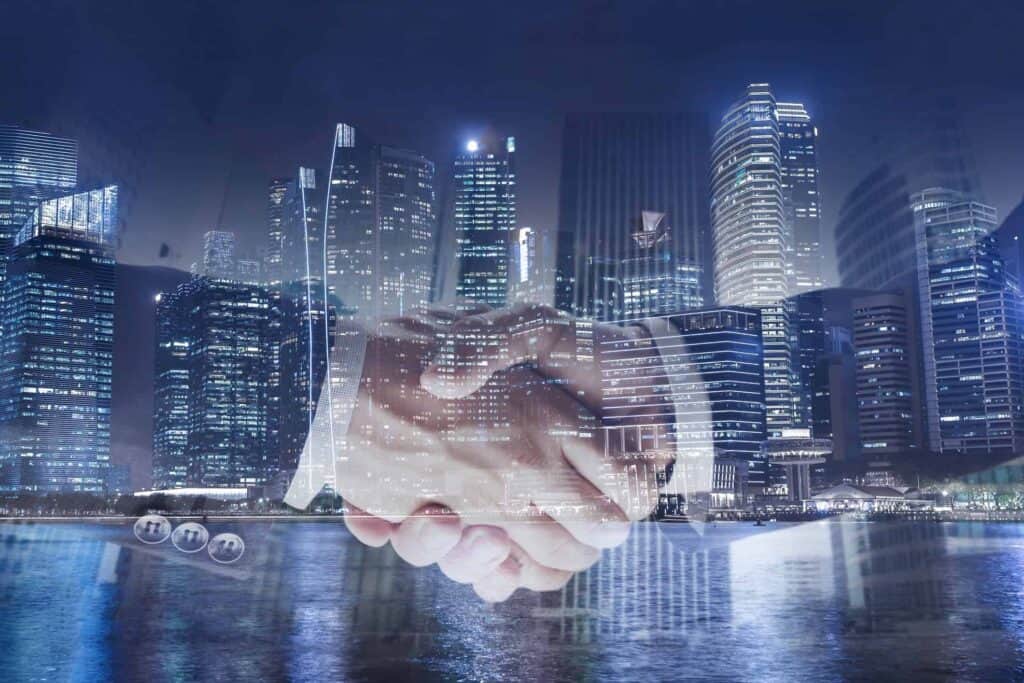
INCIT and Eficens Systems Announce Strategic Partnership to Accelerate Global Industrial Transformation
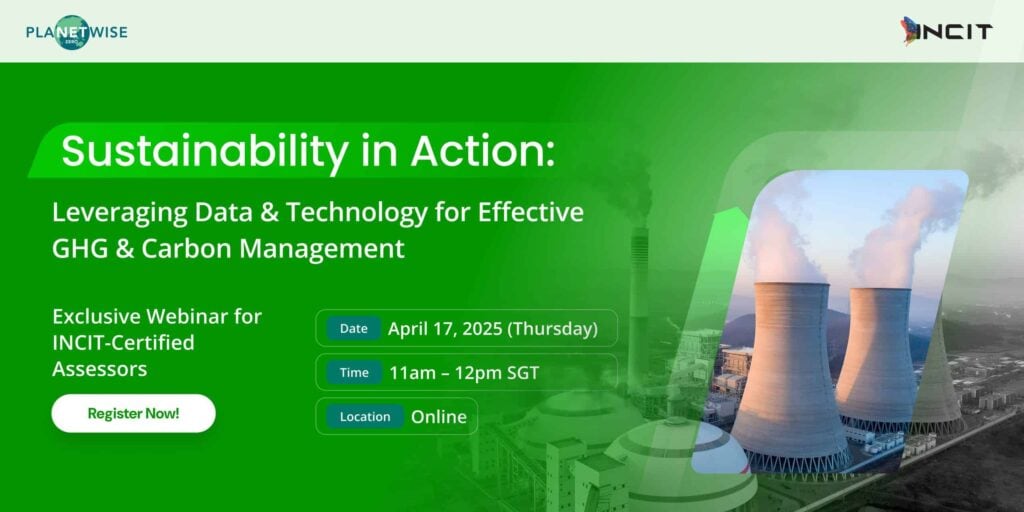
Sustainability in Action: Leveraging Data & Technology for Effective GHG & Carbon Management
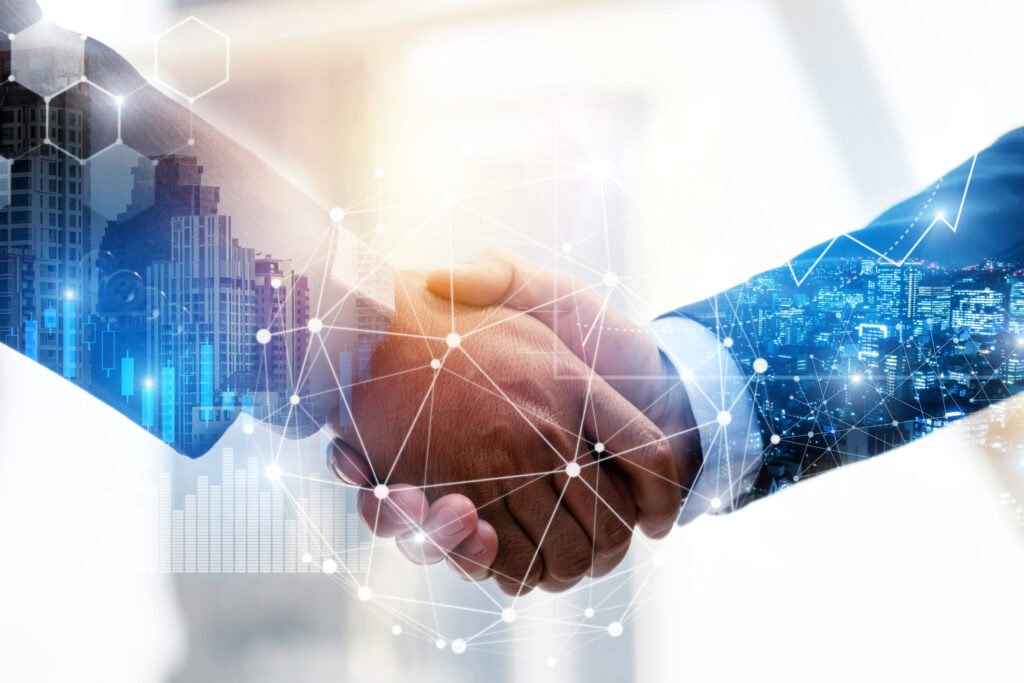
Hitachi and INCIT Partner to Advance Digital Transformation with Smart Industry Readiness Index (SIRI) and XIRI-Analytics
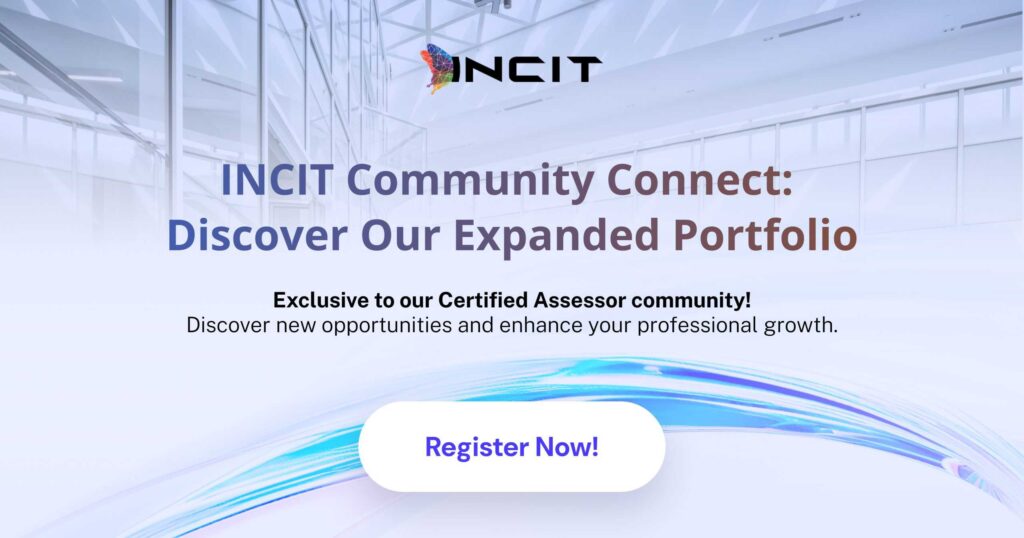
Strengthening Partnerships: INCIT Announces Exclusive Webinar for Assessor Community on Portfolio Expansion
Achievements
in numbers
Industry X.0 and Sustainability improvements worldwide
Discover INCIT
We empower manufacturers worldwide to grow, innovate, and thrive
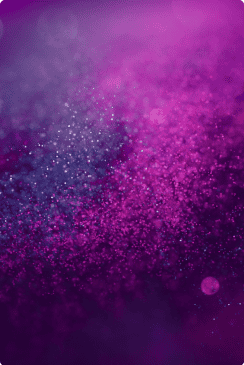
WHO WE ARE
We are committed to delivering tangible value and empowering
manufacturers in every part
of the world.
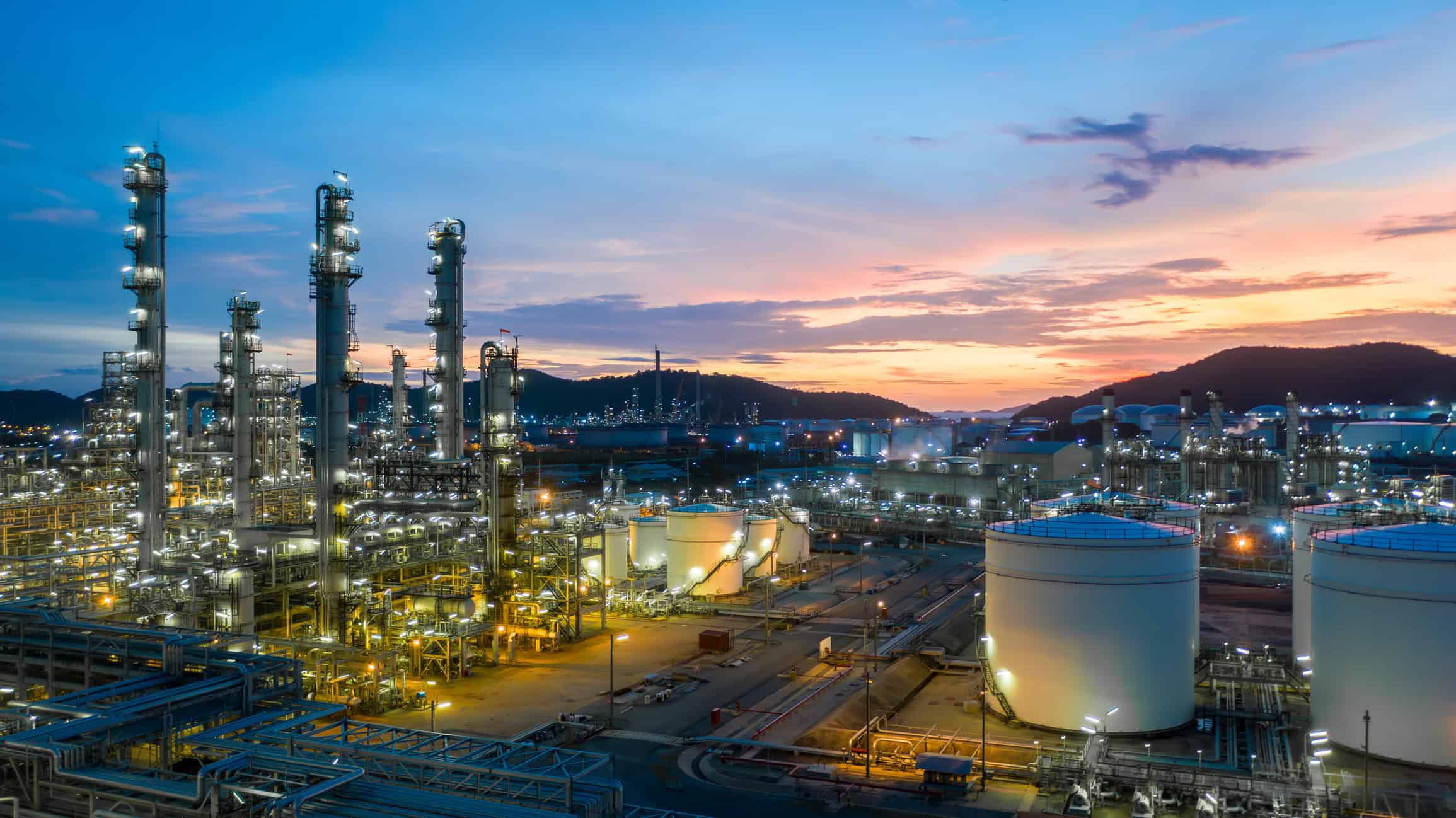
WHAT WE DO
From prioritisation indexes to industrial expertise, we are the ideal partner for driving positive change worldwide.
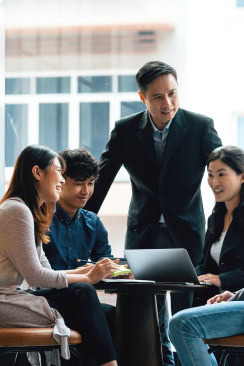
PARTNERSHIP MODEL
Partners are at the heart of everything we do. Discover how we work with our partners to achieve mutual success.
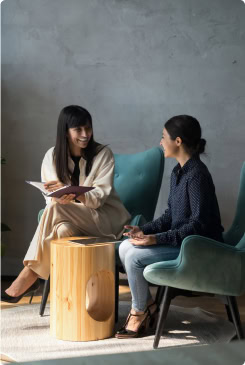
CAREERS
Join us and be part of the team accelerating industrial transformation worldwide.